An Unbiased View of Alcast Company
An Unbiased View of Alcast Company
Blog Article
Get This Report about Alcast Company
Table of Contents8 Easy Facts About Alcast Company ExplainedExcitement About Alcast CompanyFascination About Alcast CompanyThe 7-Second Trick For Alcast CompanyThe Greatest Guide To Alcast Company7 Simple Techniques For Alcast Company
Chemical Comparison of Cast Light weight aluminum Alloys Silicon advertises castability by lowering the alloy's melting temperature and improving fluidness during spreading. Additionally, silicon adds to the alloy's stamina and use resistance, making it useful in applications where toughness is crucial, such as automotive components and engine elements.It additionally improves the machinability of the alloy, making it simpler to refine right into completed items. In this means, iron adds to the total workability of aluminum alloys.
Manganese adds to the stamina of aluminum alloys and enhances workability. Magnesium is a lightweight aspect that provides strength and impact resistance to aluminum alloys.
Some Known Incorrect Statements About Alcast Company
It allows the production of light-weight components with exceptional mechanical properties. Zinc boosts the castability of light weight aluminum alloys and aids manage the solidification process during spreading. It improves the alloy's toughness and solidity. It is usually located in applications where detailed forms and fine details are needed, such as decorative castings and specific automotive components.

The key thermal conductivity, tensile toughness, yield stamina, and elongation vary. Select suitable basic materials according to the performance of the target item created. Amongst the above alloys, A356 has the greatest thermal conductivity, and A380 and ADC12 have the cheapest. The tensile restriction is the opposite. A360 has the most effective return strength and the highest possible prolongation rate.
9 Simple Techniques For Alcast Company
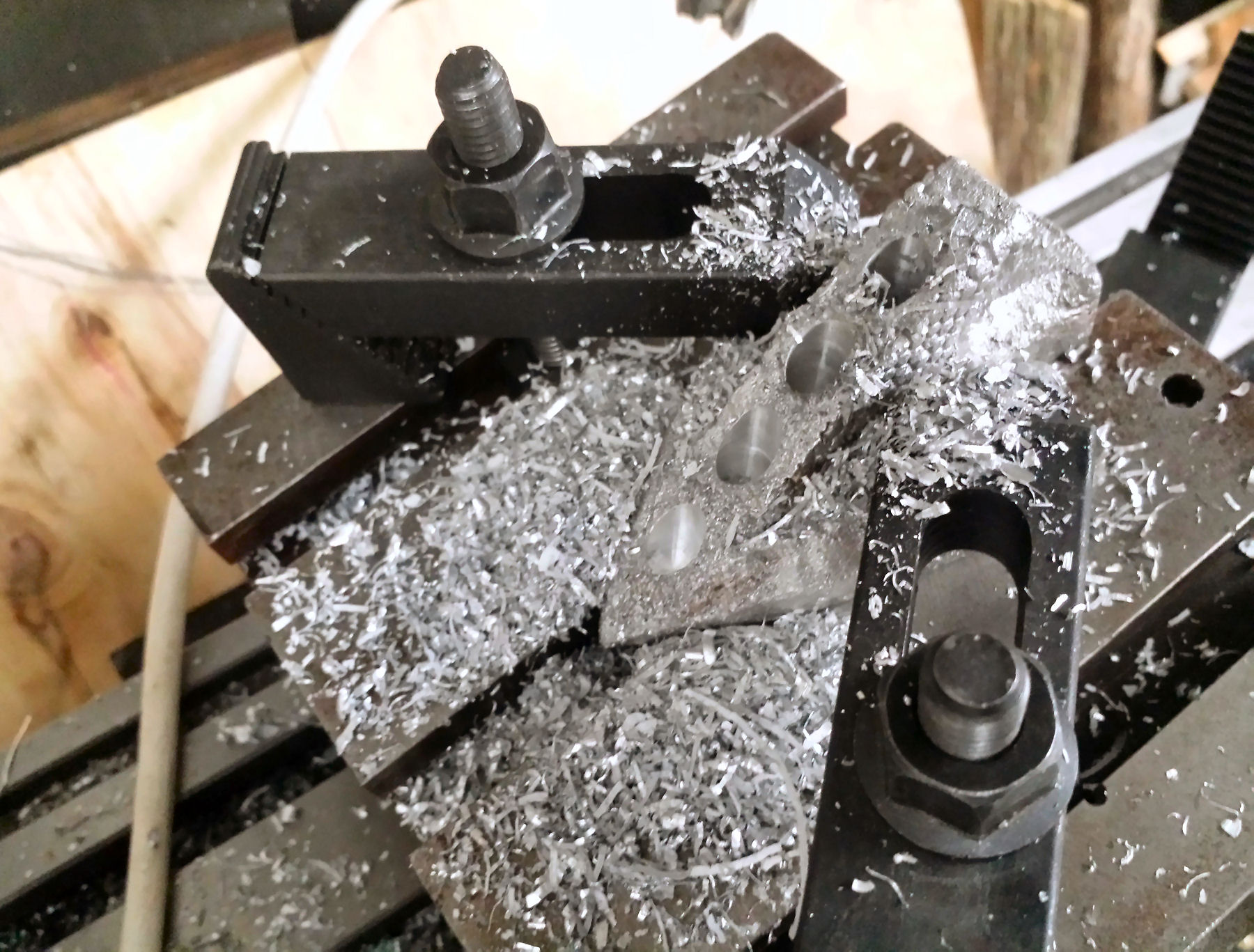
In precision spreading, 6063 is appropriate for applications where detailed geometries and premium surface coatings are paramount. Instances consist of telecommunication enclosures, where the alloy's superior formability permits sleek and visually pleasing layouts while keeping structural stability. In the Illumination Solutions industry, precision-cast 6063 elements produce classy and efficient lighting components that require elaborate forms and good thermal efficiency.
The A360 shows superior prolongation, making it excellent for facility and thin-walled components. In accuracy spreading applications, A360 is appropriate for sectors such as Consumer Electronic Devices, Telecommunication, and Power Devices.
The 9-Minute Rule for Alcast Company
Its one-of-a-kind homes make A360 a useful choice for precision casting in these markets, enhancing item durability and top quality. aluminum foundry. Light weight aluminum alloy 380, or A380, is an extensively made use of spreading alloy with several distinct qualities.
In accuracy spreading, aluminum 413 beams in the Customer Electronic Devices and Power Tools sectors. It's frequently utilized to craft elaborate parts like smartphone real estates, electronic camera bodies, and power device housings. Its precision is impressive, with limited tolerances as much as 0.01 mm, making sure remarkable product assembly. This alloy's exceptional deterioration resistance makes it a superb selection for outside applications, making certain durable, durable products in the pointed out sectors.
3 Simple Techniques For Alcast Company
The light weight aluminum alloy you choose will considerably influence both the casting procedure and the homes of the final item. Because of this, you must make your choice very carefully and take an informed method.
Identifying the most appropriate aluminum alloy for your application will certainly mean evaluating a wide array of features. The first classification addresses alloy attributes that impact the production process.
Examine This Report on Alcast Company
The alloy you pick for die spreading directly affects several elements of the spreading process, like exactly how very easy the alloy is to work with and if it is susceptible to casting flaws. Warm breaking, additionally called solidification breaking, is a normal die casting defect for aluminum alloys that can result in internal or surface-level splits or cracks.
Particular aluminum alloys are a lot more susceptible to hot fracturing than others, and your selection must consider this. One more usual problem discovered in the die casting of aluminum over here is die soldering, which is when the actors sticks to the die wall surfaces and makes ejection difficult. It can damage both the actors and the die, so you need to try to find alloys with high anti-soldering properties.
Corrosion resistance, which is currently a remarkable attribute of aluminum, can differ substantially from alloy to alloy and is a crucial particular to take into consideration depending upon the ecological problems your product will certainly be subjected to (aluminum foundry). Put on resistance is another building frequently sought in aluminum products and can separate some alloys
Report this page